How Cold Cutting is Revolutionizing Manufacturing
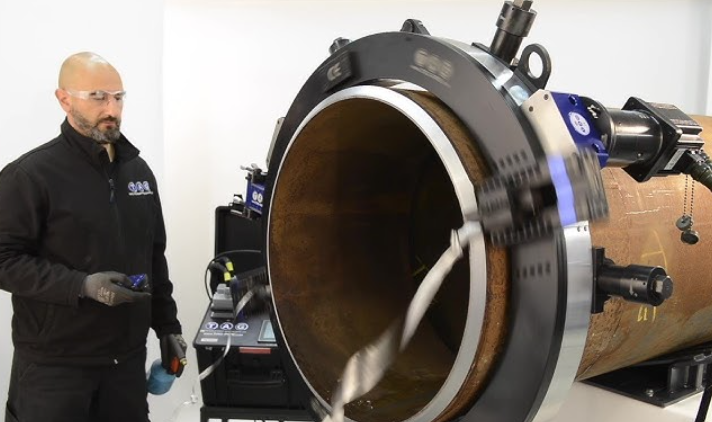
In the grand scheme of industrial evolution, manufacturing methods have advanced significantly from the days of manual labour and rudimentary tools. Precision and efficiency are now critical factors in the production process, leading to the evolution of innovative technologies such as cold cutting.
In this article, we will explore the concept of cold cutting, its impact on manufacturing, and its benefits and applications in various industries.
Contents
Understanding Cold Cutting
At its core, cold cutting is a process that separates material from a workpiece without using a significant amount of heat. This distinction is vital, as traditional methods such as oxy-fuel cutting or plasma cutting rely on intense heat, which can lead to thermal distortion in the workpiece. On the other hand, cold-cutting technologies like waterjet and laser cutting offer a means to achieve high precision and edge quality without causing structural damage to the material.
Principles of Cold Cutting
Cold cutting encompasses a range of technologies, all with specific applications and advantages. The underlying principle is one of kinetic energy transfer – be it in the form of a high-pressure water jet loaded with abrasives or an intensely focused beam of coherent light, the energy is applied at the exact point where the cut is to be made, swiftly and cleanly, with no need for tempering or annealing post-cutting.
Benefits of Cold Cutting
The shift towards cold cutting isn’t just a quirk of modern manufacturing; it’s a strategic move to gain many benefits that traditional methods can struggle to provide.
Precision and Accuracy
Cold cutting excels at cutting intricate patterns or maintaining tolerances within micrometres. The precision these methods offer is a byproduct of their non-thermal nature; since there’s no heat-affected zone, the cut’s metrics remain precise from edge to edge.
Reduced Material Waste
Precision in manufacturing isn’t just about quality; it’s also about economizing on materials. By reducing waste through precise cutting, manufacturers can enjoy the two-fold benefits of sustainability and cost savings.
Enhanced Safety Measures
Safety is always a priority in manufacturing, and traditional cutting methods can be hazardous, releasing fumes and posing a fire risk. Cold cutting significantly minimizes these dangers, making the shop floor safer for workers.
Applications in Manufacturing
Cold cutting is used in an array of industries, each harnessing its benefits for specific use cases.
Aerospace Industry
In the precision-driven aerospace industry, where any form of distortion can have catastrophic consequences, cold-cutting techniques are extensively used to shape components and build structures for aircraft and spacecraft.
Automotive Sector
From chassis to components, the automotive sector prizes precision and material integrity. Cold-cutting methods enable the industry to produce the intricate parts needed for modern vehicles at scale and with consistent quality.
Construction Field
Construction equipment and heavy machinery components demand durability without compromise. Cold cutting maintains the balance between sturdiness and precision, even when working with hardened steel and composites.
Comparison with Traditional Methods
A key advantage of cold cutting over traditional methods is that it often eliminates or reduces the need for secondary machining operations. This streamlining saves time and simplifies the manufacturing process, potentially cutting costs significantly.
Efficiency and Cost-Effectiveness
The efficiency of cold-cutting methods is not just in their speed but in the cost savings generated by reduced post-cutting work and the ability to process a broad range of materials without retooling or setup changes.
Future Trends and Innovations
Much like the future, it’s helping to build, the cold-cutting industry is far from static. It constantly seeks to integrate innovations that push the boundaries of efficiency, safety, and environmental responsibility.
Integration of Automation
The future of manufacturing is synonymous with automation, and the cold-cutting industry is no exception. Integrating robotics and CNC systems allows for round-the-clock operation, where precision and consistency are maintained at a level that exceeds human capability.
Environmental Sustainability
With a global focus on environmental sustainability, cold-cutting methods that utilize water as a cutting medium are finding increased favour. They offer clean, digital-friendly processing and minimize the ecological footprint of manufacturing activities.
Conclusion
Cold-cutting technologies, particularly those offered by a specialized waterjet company, are pivotal in advancing the manufacturing sector towards more sustainable and efficient practices. By optimizing cold-cutting techniques, these companies not only enhance the quality and precision of the products created but also contribute to the overall reduction of the industry’s environmental impact. As we look to the future, the collaboration between manufacturers and such innovative service providers will undoubtedly be a key driver in improving production methodologies, further solidifying the importance of cold cutting in the global manufacturing landscape.